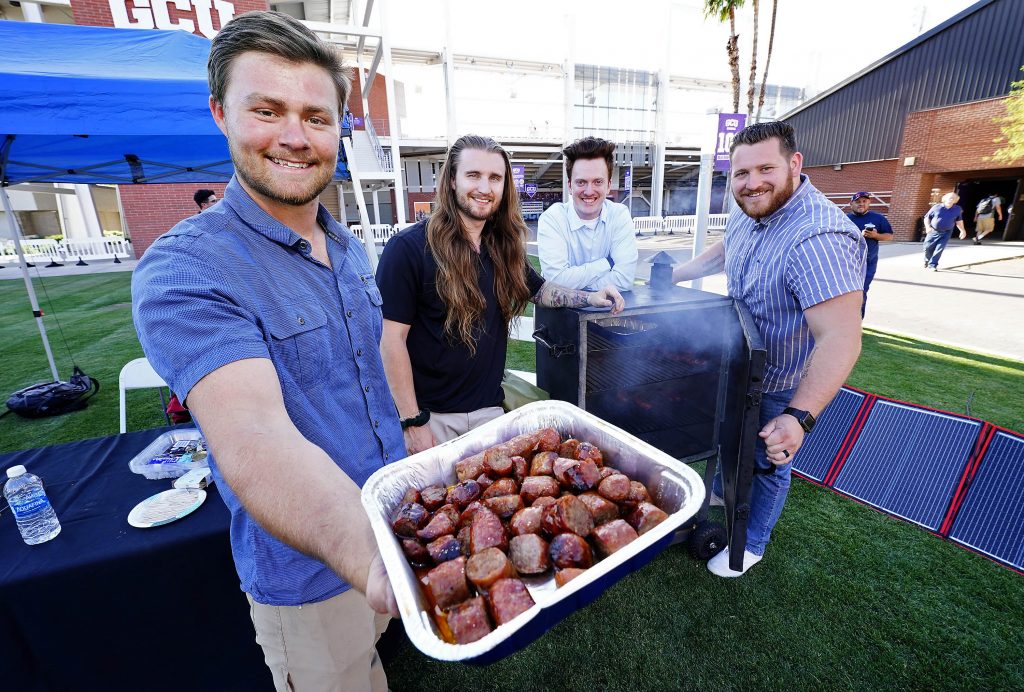
Photos by Ralph Freso / Slideshow
Grand Canyon University engineering technology students: They have the meats.
And at Monday’s Engineering Capstone Showcase, not only did they have the meats, but they displayed their innovative gumption with a fully automated solar smoker that fed not just their minds but their bellies this semester.
Was it merely the love of barbecue that inspired the team to build a smoker for their capstone project?
“That and there wasn’t really any off-grid or tailgating application for an automated smoker without having to lug around a generator and everything,” said mechanical engineering technology senior Peyton Seeger of the cooker he designed and built with teammates Dawson Buckley, Luke Griffin and Anthony Downey. “… We really, really liked the idea of the outdoors but not being limited to what you can do in the outdoors.”
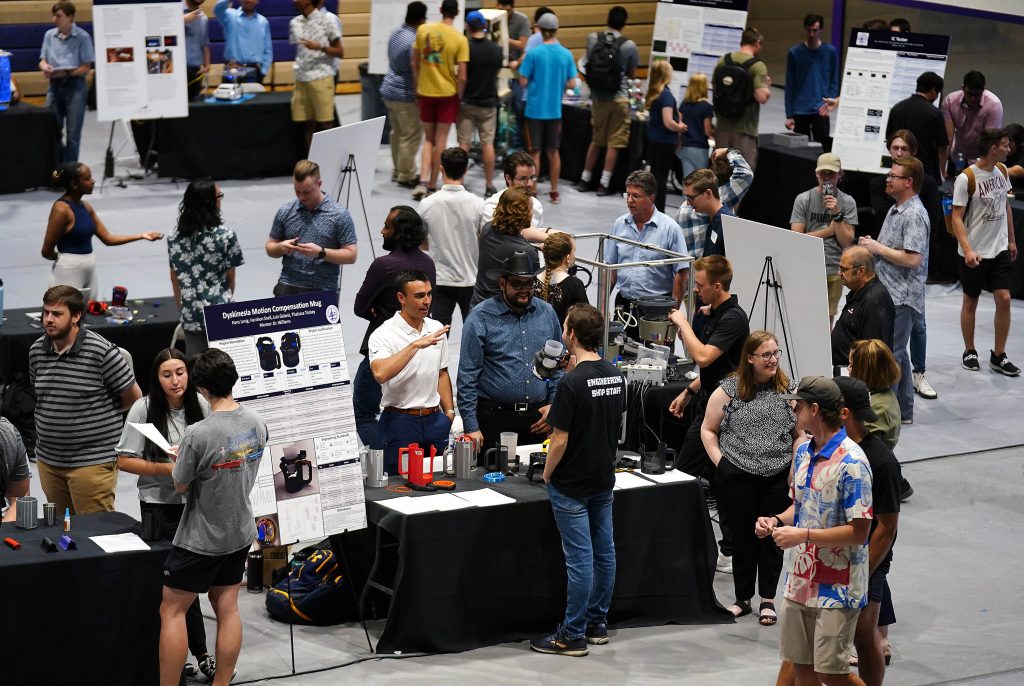
The advantage of the smoker? Since it’s automated, you don’t have to tend to it, it holds heat extremely well, and cooks have a readily available power source in the sun.
The disadvantage: Your readily available power source isn’t always available. No sun, no meats, all sadness, though at the showcase, the team offered plenty of smoker-cooked sausage to share with attendees.
The smoker was just one project among more than 30 that spanned Antelope Gymnasium and the adjacent baseball field patio lawn that College of Science, Engineering and Technology students created in their capstone course. Capstone projects, completed over two semesters, are designed so students can apply concepts and principles they’ve learned over their four years of college in the form of an end-of-program project.
While most ideas were generated by the students, some were suggested by industry, such as an automatic robot charging station for Benchmark. Others were built for nonprofits, such as a nonverbal emotional detection device for ACCEL, a school for those with disabilities.
The GCU community, board members and industry visitors also could view everything from elbow and ankle braces to a foldable longboard to extendable mountain bike handlebars.
Though, if you wanted to stay in the food and drink realm, a stop at the Dyskinesia Motion Compensating Mug table was a must.
Students designed a mug container to help patients who suffer from dyskinesia, or muscle tremors.
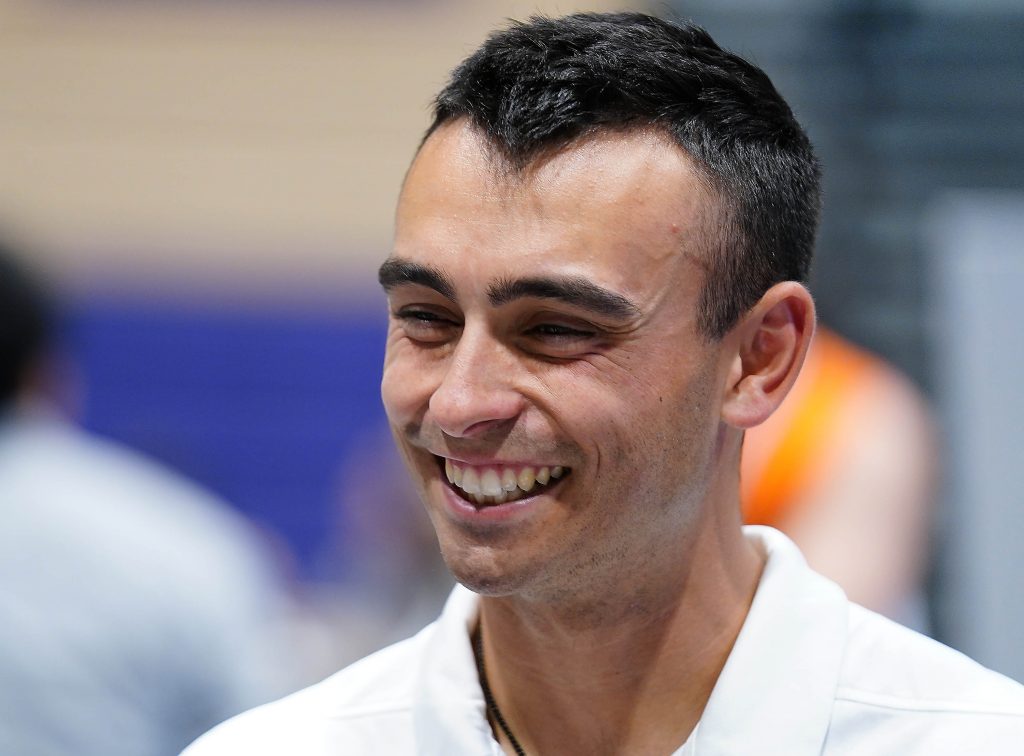
“People with Parkinson’s are suffering from muscle tremors to the point where, when they’re holding a cup, they can’t control it themselves or they can only fill it up a small amount,” said Harrison Snell, who knows firsthand how dyskinesia can affect a patient’s life — his mom has multiple sclerosis.
The team went through six iterations of the assistive device, which can sense its own position and works to counteract imbalances. The final design is 3D-printed out of carbon fiber and is so strong it survived 14 drop tests.
One of the challenges for the team, made up of mechanical and biomedical engineering majors, is it didn’t have an electrical engineer.
“We’d never made circuits like this before,” Snell said, but in the end, they ended up with a workable device. That learning curve turned out to be valuable.
“You can learn a heck of a whole lot by just Googling and asking questions and working with other people.”
One of the goals of the capstone projects is for engineering students from various disciplines to work together, just as they will in their professional careers. Engineering is a field heavy on teamwork.
“I look for how well students work with different types of students,” said Antonio Garcia, an Engineering Advisory Board member who was on the GCU campus for the first time and was attending his first CSET Engineering Capstone Showcase. “You see that here, so that’s very exciting.”
Teamwork played a big part in a goalie helmet designed by a group of mechanical, general and biomedical engineers.
They wanted to create a hockey helmet that would better protect players from concussions.
“I actually play for GCU hockey,” said mechanical engineering senior Gabriel Lepper, a goalie who has suffered concussions from playing the game.
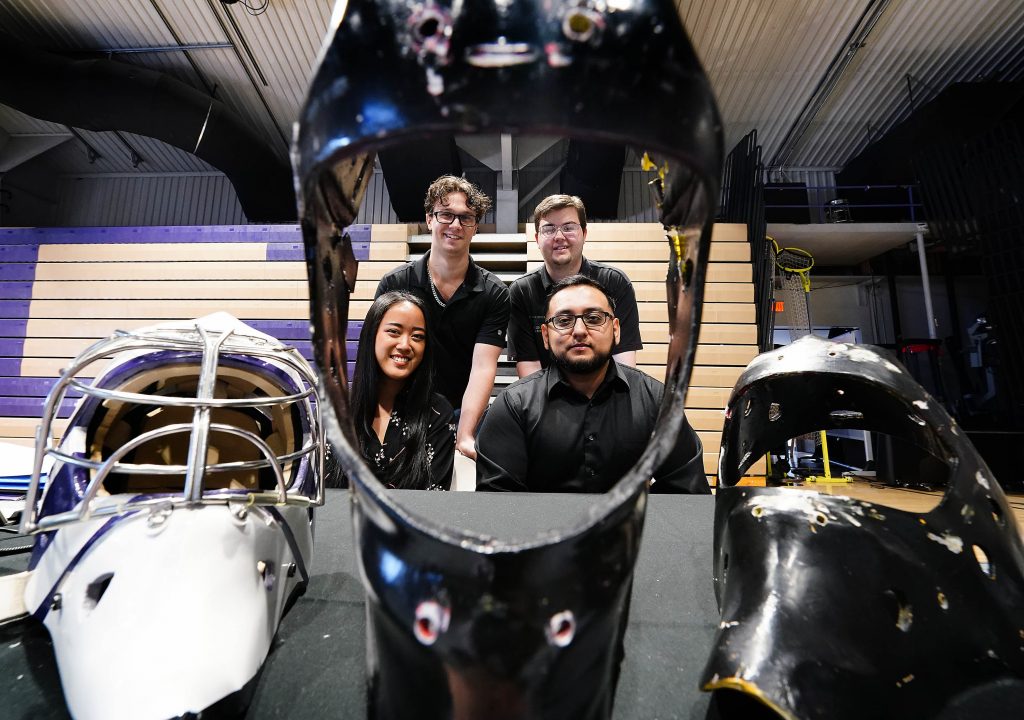
Lepper said the speed of shots are getting faster, and while companies are designing better chest pads and knee pads, the helmet hasn’t received the same kind of industry attention.
The team showcased the third iteration of its helmet. The shell is made of 3D-printed carbon fiber filament wrapped in fiberglass, and the interior includes three layers of padding inside and impact-absorbing gel.
The helmets were tested in the baseball field batting cages with objects hurled at them at 85 to 130 miles an hour.
Two teams took on the challenge presented to them by Electrical Engineering Professor Dr. Samantha Russell to come up with a better design for drywall stilts.
Mechanical engineering major Max Escobedo has worked in the drywall industry, so he had a passion for this project.
The goal was to design stilts that could raise up and down electronically with the worker still on the stilts. Escobedo’s team placed a ball screw mechanism in the stilts that can be activated by a microcontroller.
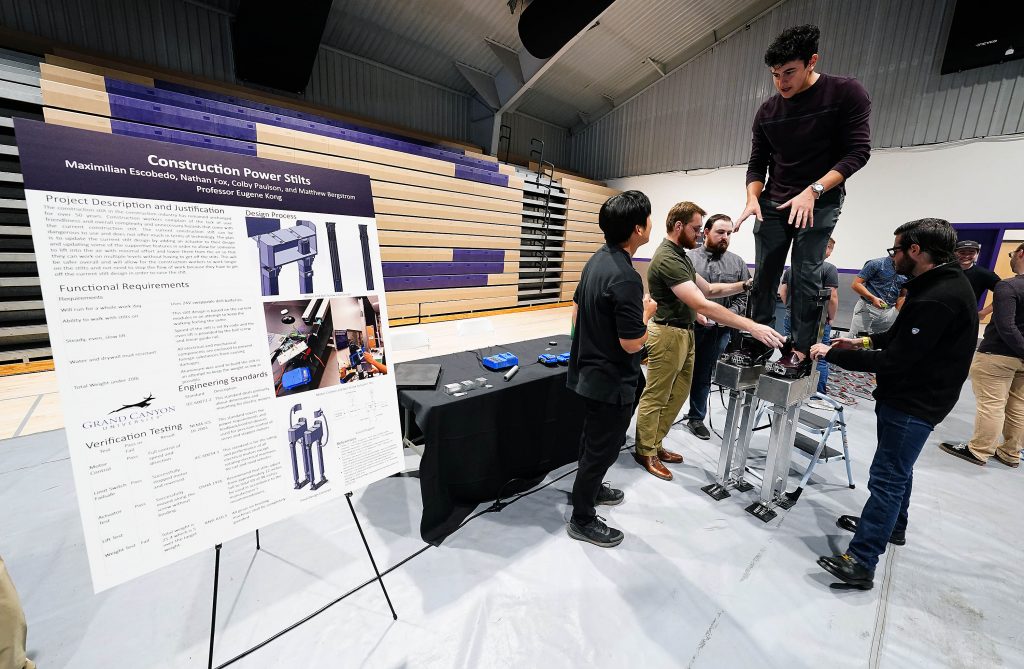
To improve their design, team members said they would make the stilts lighter in weight because some heavy components are affecting its walkability. They also would like to widen the foot base to increase stability.
For Escobedo, working with CNC machines to create some of the metal pieces on the stilts was the most fun.
“I personally think a lot of the fun of it, too, is the problem-solving,” added teammate Nathan Fox, who said one of the last additions the team made was putting a structural support in the stilts in which the ball screw sits.
Jonathan Juarez and his team on the Mobile Trash Collector project would agree.
His group built a trash-collecting robot that, from its docking station, finds a trash wagon, connects to it via magnet then empties trash into the wagon by way of a robot arm. It can pull up to 45 pounds of trash.
Juarez said the project is a two-year project and that the next team would add QR codes and cameras to make the robot more autonomous.
The biggest challenge the group had was integrating everything together. Sometimes the robotic arm would work but the docking system wouldn’t and vice versa.
“But to be honest, integrating was still the most fun,” said teammate Kamsiyochukwu Okonkwo. After solving the problems, “when it starts working, you feel like you’re on top of the world," stilts or not.
Manager of Internal Communications Lana Sweeten-Shults can be reached at lana.sweeten-shults@gcu.edu or at 602-639-7901.
***
Related content:
GCU Today: Hands-on engineering capstones get thumbs up
GCU Today: GCU helps school engineer a brighter future
GCU Today: Engineering shops, clubs show what they can do
GCU Today: KEEN honoree drives excellence in teaching