By Rick Vacek
GCU News Bureau
The Grand Canyon University campus is a quiet, peaceful place these days, save for the usual whirs and beeps and thwap-thwap-thwaps of construction.
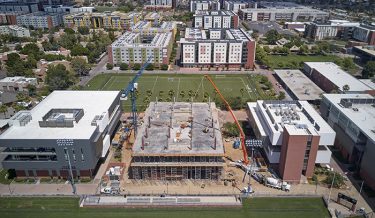
But excitement has been rising for employees in the Student Life and College of Humanities and Social Sciences buildings. They have a front-row seat as the Student Advising Services Building, the most challenging construction project ever undertaken at GCU, grows skyward.
It has created a renewed appreciation for the skill required to take on something of this magnitude. And, inevitably, the curiosity builds into questions:
“When did they pour the concrete for that floor?”
“How does it not stick to the wood platforms below it?”
“What is the purpose of that wiring that the concrete is poured over?”
“How do they get all those concrete columns to be the exact same height?”
But the consternation goes beyond concrete. There’s also the human side:
“What hours do they work?”
“How do they deal with the heat?”
“How long does the crane operator have to stay in that little cab way up in the sky … with no bathroom?”
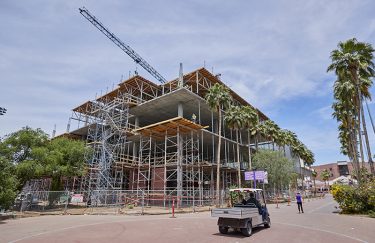
And, quite simply:
“How do they do that?”
“How do they KNOW?”
So this is a story for all those amazed employees and anyone else wondering how Pono Construction, the University’s building partner since it erected the North Rim Apartments in 1986, does it. Like the new building, we’ll go from the ground up on a tour guided by Pono owner Butch Glispie, who said he visits every construction project on campus at least once each day.
First, it’s important to understand why this build is so complicated and how Pono is facilitating the construction.
Because the building is positioned between the two four-story structures to the north and south and the Promenade and GCU Stadium to the east and west, getting trucks and cranes into the area is challenging. The walkway east and south of the stadium had to be closed to create access, but it’s still an extremely tight turn.
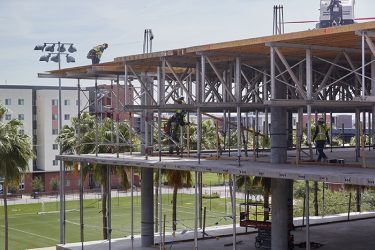
Equally tight – for both the crane operator and Student Life Building employees looking through their windows – is the process of swinging the preconstructed wooden platforms, called tables, into position so that a new floor can be built. It’s hard not to notice when such a massive structure is just a few feet from you as a worker uses a rope to guide it into place, but they make it look easy.
The tables come in various sizes depending on where they sit in the building, and as each floor is completed, the tables are transferred to the next floor up.
The building is what is known as post-tension, which the Concrete Construction website describes as a “method of reinforcing concrete (that) enables a designer to take advantage of the considerable benefits provided by prestressed concrete while retaining the flexibility afforded by the cast-in-place method of building concrete structures.”
The five-story Student Advising Services Building will be the tallest post-tension structure on campus.
“Most of the high rises you see going in downtown are like that,” Glispie said. “It’s faster and cheaper than steel.”
The concrete floors are poured overnight for two reasons: the cooler temperatures and the lack of rush-hour traffic. The concrete trucks need to get through in a timely fashion for the task to be properly fulfilled. Concrete work is tricky.
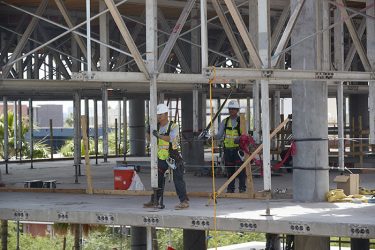
“Suntec Concrete, which does all of our structural stuff on campus, has probably got the most robust training program of anybody I’ve seen,” Glispie said. “If you go to work as a laborer there and you put in the time, they hold classes during the week and on weekends. If you’re willing to sit and go through the classes, you can advance quickly with them. But you cannot advance if you don’t get the training. It IS complex.”
And how does the concrete not stick to the tables?
“They spray a form release on it, but the top of it is a special form – it’s not just plywood,” Glispie said. “It’s got a plastic coating on it, and it’s made to be reused.”
But a lot of preparation is required before the trucks can roll. All that rebar wiring must be carefully laid from one side to the other, a process that takes about 10 days per floor.
“You see those blue-coated strands? That’s a plastic sleeve that’s greased, and there’s a steel cable in there,” Glispie said. “That gets placed in a draping motion, and then after the concrete is placed and it reaches at least 70% strength, we come back and tension that to a predetermined amount with a little device that they hook onto the end of it.
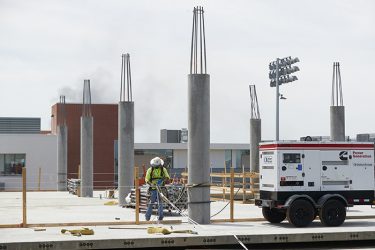
“That’s what actually holds that floor up – it’s a much quicker way to go, and it takes out probably half the steel in the floor. The floor is somewhat flexible, too, so it doesn’t tend to crack or give way. And it’s a really adaptable building, after the fact, because we don’t need any walls for support. Fifteen years from now if somebody says, ‘I want to repurpose that building,’ they literally could strip every wall out of the inside of that and reconfigure it. All of the forces are on the columns.”
The columns – 24 on each floor – go up first, and by now the ogling employees have the process memorized: The rebar cages are positioned, the form-fitting sheath (again, the form-release spray ensures that the concrete won’t stick to it) is snapped into place and then the concrete-pouring tube is raised by the long arm of the crane-like truck below to fill the column to the required height.
But how do they know that height?
“We have a benchmark outside on the ground,” Glispie said. “It’s a known elevation. We keep coming back to that as it goes up.”
When the concrete for the third floor was poured, the masonry began at the ground level. The reason: The third floor is cantilevered, which means it extends out farther than the floors below it.
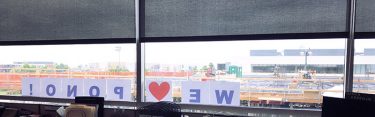
“Because it’s got that cantilevered section, they’re safe under there,” Glispie said. “They don’t have something above them that’s going to fall on them and hurt them.”
Brickwork for the elevators, stairwells and some outside walls already are in place several floors up, and this is where it gets interesting. The roof will slope to the center, which means the tables will have to be rearranged to create slope in the concrete.
There are about 75 workers at the building on a normal day, and they’re out there six days a week. Most of them start their shifts at 5 a.m. – unless, of course, they’re helping with the overnight pour of a concrete floor – but they could get going even earlier in a few weeks when daytime temperatures climb to triple digits before noon.
Getting the attention of the construction workers, most of them protected head-to-toe from the sun, has become a sort of sport in the nearby buildings. A “We Love Pono” sign on the fourth floor of the Student Life Building was met with particular glee.
“The guys appreciated that – it got a lot of comments,” Glispie said. “Most construction workers don’t ever get a thank-you. The sad thing is that by the time someone gets in and gets to enjoy building, the construction workers are long gone.”
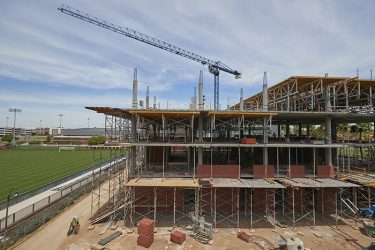
We saved the most important answer for last. Student Life Building employees have watched in fascination as the crane operator climbs the ladders inside the gridwork of the narrow blue tower, which was erected in just one day.
It’s so high, it almost feels as if it would take most of a day to get down from that perch. That has sparked the inevitable question: What if nature calls when he’s sitting in the cab six stories up?
“I’m guessing he doesn’t drink a lot of coffee in the mornings,” Glispie said, laughing. “At least he’s got an air-conditioned spot up there.”
The AC will give him a decided advantage over the workers below during the summer months. The heat will be on to finish the new home of the Antelope Reception Center, Enrollment and other departments before the end of the year. So what’s next?
“Masonry will start coming up, and the light-gauge steel stud framing will start, and that will then start closing in the outside of the building,” Glispie said. “Then you’ll see some fiberglass drywall go on that on the outside. There’s a combination of metal panels and stucco that go in various places on that. At about that same time, the window guy will get in there.”
That, no doubt, will spark more questions from the onlookers next door, so riveted by the process that groups of five and 10 often have watched in fascination.
“It’s going to be a nice-looking building,” Glispie said.
No question about that.
Contact Rick Vacek at (602) 639-8203 or rick.vacek@gcu.edu.