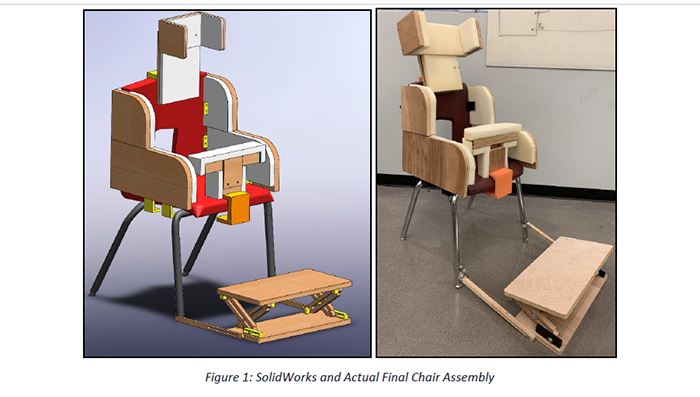
By Lana Sweeten-Shults
GCU News Bureau
Noah Hibdon knew which capstone project was the right fit for him: one that would help the special needs community.
“I actually have a brother with Down syndrome,” said Hibdon, a senior mechanical engineering major at Grand Canyon University.
He was one of about 135 engineering and engineering technology students on more than 30 teams who presented their final projects virtually at Monday’s Engineering Capstone Showcase. The event, organized by the College of Science, Engineering and Technology and Strategic Employer Initiatives, spotlights everything students have learned over their four-year trek at GCU. They put all their knowledge and skills to work in one academic, career-culminating project.
It's a yearlong endeavor – students design and plan their projects in the fall and then execute those designs in the spring – that comes to an end at the showcase, attended not just by students’ professors and others in the GCU community but by industry professionals, family, friends and prospective students.
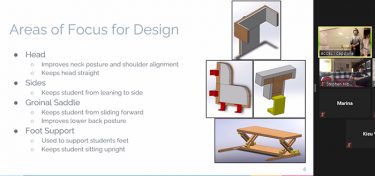
Hibdon’s project, a team project with Tabitha Keating, Marina Vu and Foster Olson, focused on designing a modular adaptive seating system for students with physical disabilities.
It was just one of the projects students delved into to help the special needs community as part of a collaboration with the Arizona Centers for Comprehensive Education and Life Skills (ACCEL). The nonprofit organization serves children and adults with developmental disabilities.
“Our advisor (biomedical engineering Professor Dr. David Kwartowitz) works closely with them,” said Vu.
ACCEL contacted GCU about coming up with a chair design for students who seem to spend as much or more time focusing on their posture than they do on their coursework.
“The school already uses some adaptations for their chairs,” said Keating, a mechanical engineering major, “but they wanted a way that was very consistent and that could be taken apart off the chair and moved with the students as they grew or moved, and it could be manufactured from a variety of skillsets.”
The team focused on retrofitting existing school chairs and designing a system that would support a students’ sides, groinal saddle (to prevent students from sliding out of their chair) and feet (a foot support where students can rest their feet). Because each user is unique and the users don’t struggle with the same posture issues or sit the same way, it was important that the systems were designed and built independent of each other and were universally adaptable to fit standard school chairs.
Students created the chair system using SolidWorks and knew ACCEL has access to ShopBot and 3D printing, so they wanted to make sure their designs could be executed using those technologies.
The end product wasn’t necessarily the chair system itself but the files on how to build it.
“We wrote a book, essentially,” Olson, a biomedical engineering major, said of the manual.
Because of COVID, the capstone team couldn’t test its chair system at ACCEL, which would have been preferable. But the team members tested their design on themselves, and Hibdon said his brother tested the system, too.
“We had him seeing how it would work and how we could make adjustments based on sensory issues and whatnot,” Hibdon said.
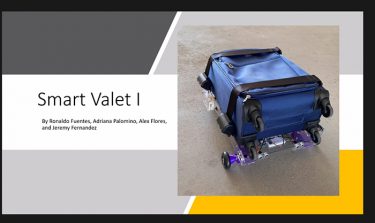
One of the virtual breakout rooms at the event featured the Smart Valet project.
Ronaldo Fuentes, Alex Flores, Jeremy Fernandez and Adriana Palomino, a team of mechanical and electrical engineering students mentored by Dr. Eugene Kong, designed an adaptable robotic cart to help travelers transport their luggage.
The adaptable cart is something travelers would attach to their luggage to create a hands-free system. The idea is for the robotic cart to follow the traveler via a Bluetooth device and an app that can be downloaded on a smartphone.
“It’s to assist people who are unable to carry their luggage by aiding them with the robotic cart to carry the luggage for them so they will be able to have more ease when they’re traveling,” Fuentes said. “It’s also true for people who have kids with them or service animals when they’re traveling.”
But more than that, Fuentes added, “The basis of our project is pretty much helping out people who do have physical limitations, who do have disadvantages. … Sometimes people with arthritis do struggle to carry their own luggage – that’s something we took into consideration. What can we make for those travelers to give them a little more freedom?”
The team members said their smart valet, powered by a lithium battery, isn’t quite fully autonomous. They would like to add more sensors to it for object avoidance. They also learned a lot about the adjustments they needed to make to their design, such as speed adjustments to different kinds of flooring.
One of the considerations the team made in the design was to include a removable and rechargeable lithium battery that could be properly stowed away to comply with FAA regulations, since lithium batteries have been prone to overheating. The team also included a safety feature in the design, a cut-off feature for the lithium battery, to protect the motor drivers by making sure the battery doesn’t fully discharge. The cut-off feature turns off the battery, too, when it is low so it isn’t drained of its power.
Fuentes’ team was one of two Smart Valet teams mentored by Engineering faculty instructor Craig Price that presented their work at the showcase. The other team included Dante De Simone, Eric Kamanzi and Sean Stouffer.
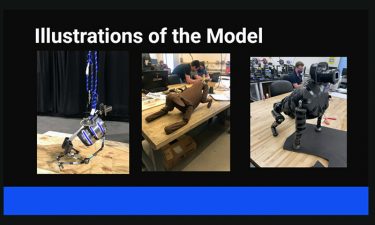
Other students developed a crash test dummy to be used to test canine harnesses. The team, which included Sebastian Fajardo, Christian Messick-Zamudio, Jake Nickoloff and Thien Nguyen, was mentored by Dina Higgins, who teaches mechanical engineering technology at GCU and worked on seatbelt design in the auto industry.
“The reason why we’re doing this is because there is no standard out there in the market that says that each one of the harnesses has been crash tested in a specific way,” said Fajardo, a mechanical engineering student.
According to the team, add-on seat belt systems for vehicles are designed to restrain pets, namely dogs. In 2020, pet restraint manufacturers began working with the American Society for Testing Standards to define a crash test standard all pet harnesses would have to pass if a system is being marketed as “crash tested.”
The team decided to work on a canine crash test dummy for a medium-size dog.
One challenge for the team was that it was hoping to work with a seatbelt harness manufacturer to test its pet crash test dummy. But Fajardo said that because of COVID-19 restrictions, the team wasn’t able to work with that manufacturer.
But the team did perform three tests of its own on a canine dummy: a center of mass test, a configuration test and a drop test.
“Overall, the dummy passed all the tests,” said Nguyen, who showed visitors video of the drop test. The canine dummy did not sustain any damage after the test, she said.
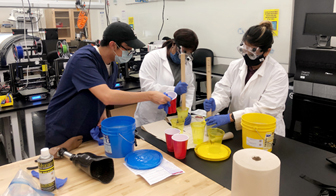
The team of Alexander Cortez, Rubi Gordillo Santana, Kamui Peeples and Yvette Nkongho worked on a project called “Automatic Prosthetic Leg Customization.”
Modern prosthetics bind to a stump using a cup fitted by a prosthetist. The fit depends on the skill of that prosthetist.
The methods currently in use to fit a prosthetic cup, from using a mold or a scanner for a fitting through computer-aided design, are time consuming, according to the team. It can take weeks for the patient to receive the prosthetic.
The team wanted to explore 3D scanning and computer-based modeling to develop a 3D printable interface for a prosthetic leg. The idea was to try to fit those prosthetics even better to minimize the abrasion and pain a patient may experience because of the fit of the cup. So they wanted to incorporate software to complete the fit by restructuring the base cup to the patient's scanned stump.
“It’s a new process of fitting a prosthetic on a patient,” said Cortez. “ … This method is going to scan it, but the software that is being created alters the cup to fit them automatically, so it’s an automatic fitting customization for the patient.”
As for so many of the engineering teams, their project wasn’t just a project.
Many of the students wanted to delve into a project with a servant mindset – to help others, whether it’s for pets or those with a disability.
“The end goal,” wrote the students who built the seating system for ACCEL, “is to serve others through the project and be a representation of why we are becoming engineers.”
Senior writer Lana Sweeten-Shults can be reached at lana.sweeten-shults@gcu.edu or at 602-639-7901.
***
Related content:
GCU Today: Students' capstones showcase creativity, tech savvy
GCU Today: GCU programs earn prestigious ABET accreditation
GCU Today: Engineering, tech students showcase their ingenuity